Dwelling Unit for Musicians by Auar
Dwelling Unit for Musicians is a modular prefab housing located in Bristol, United Kingdom, designed in 2021 by Auar.
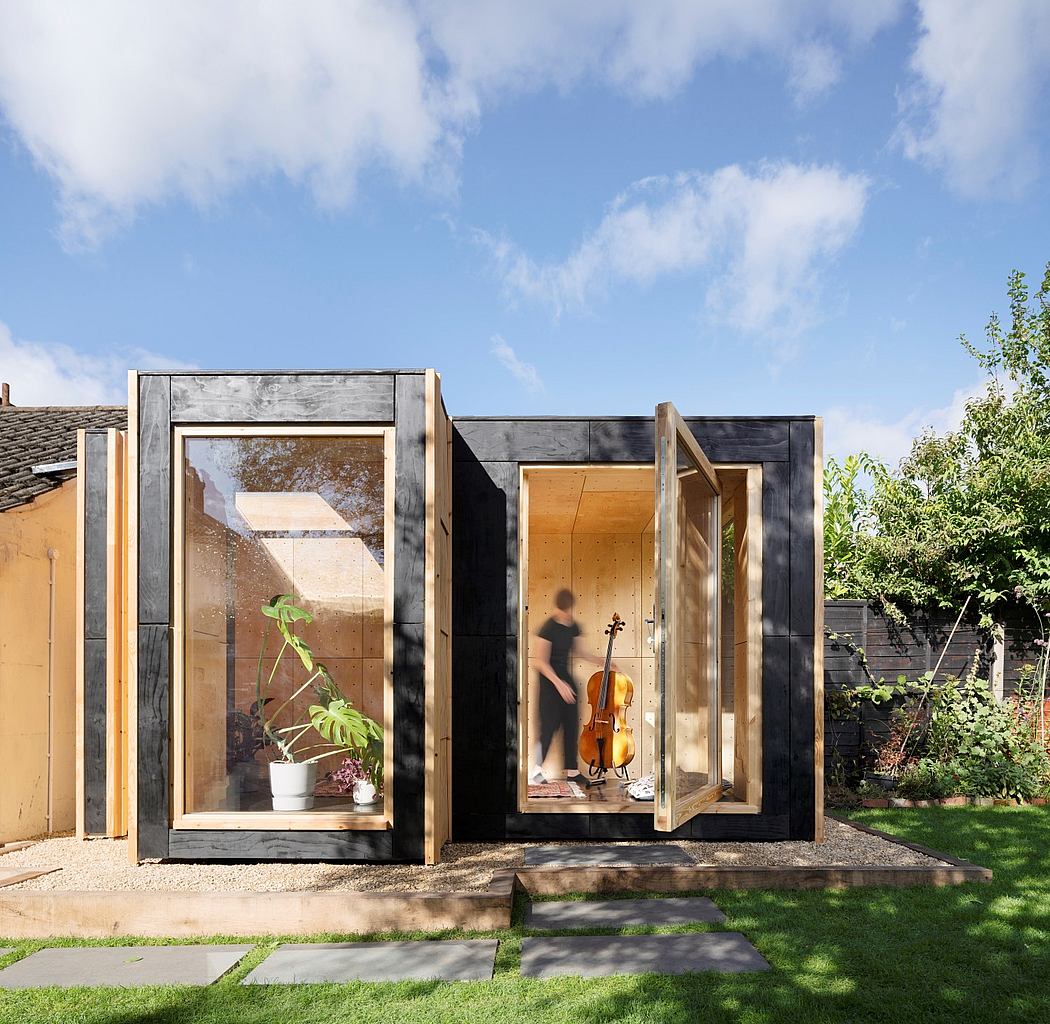
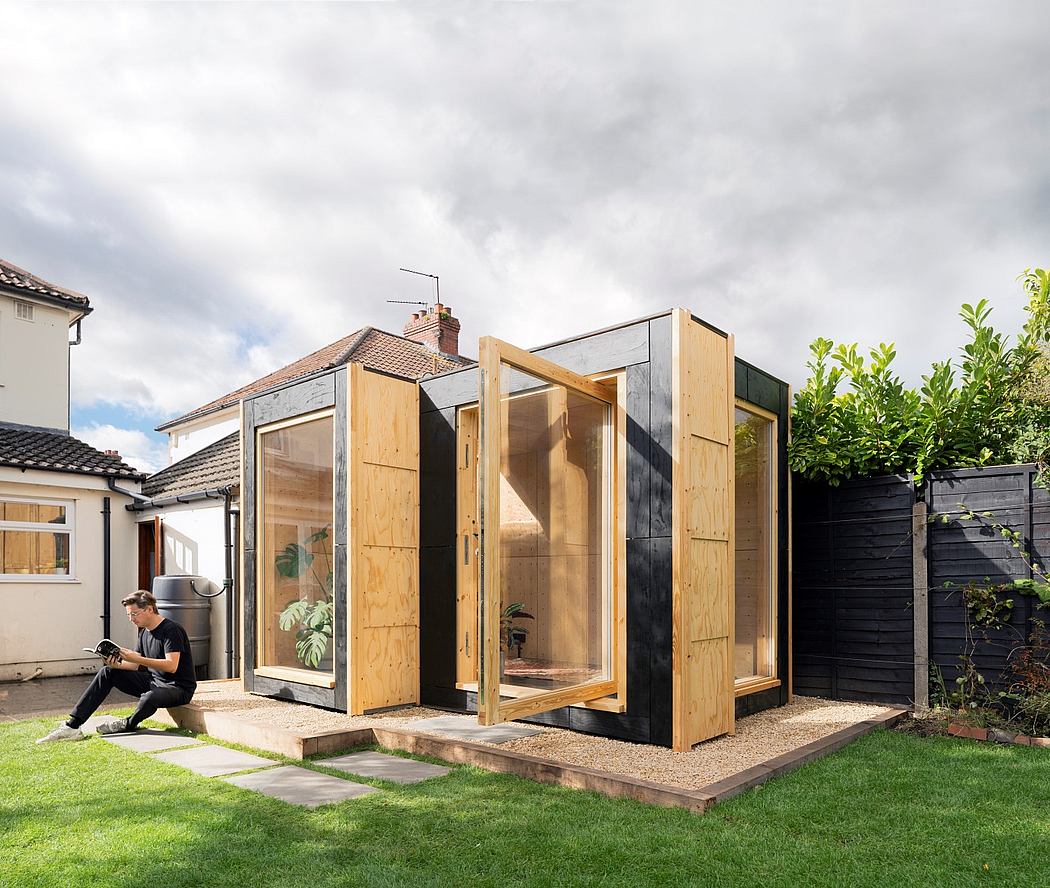
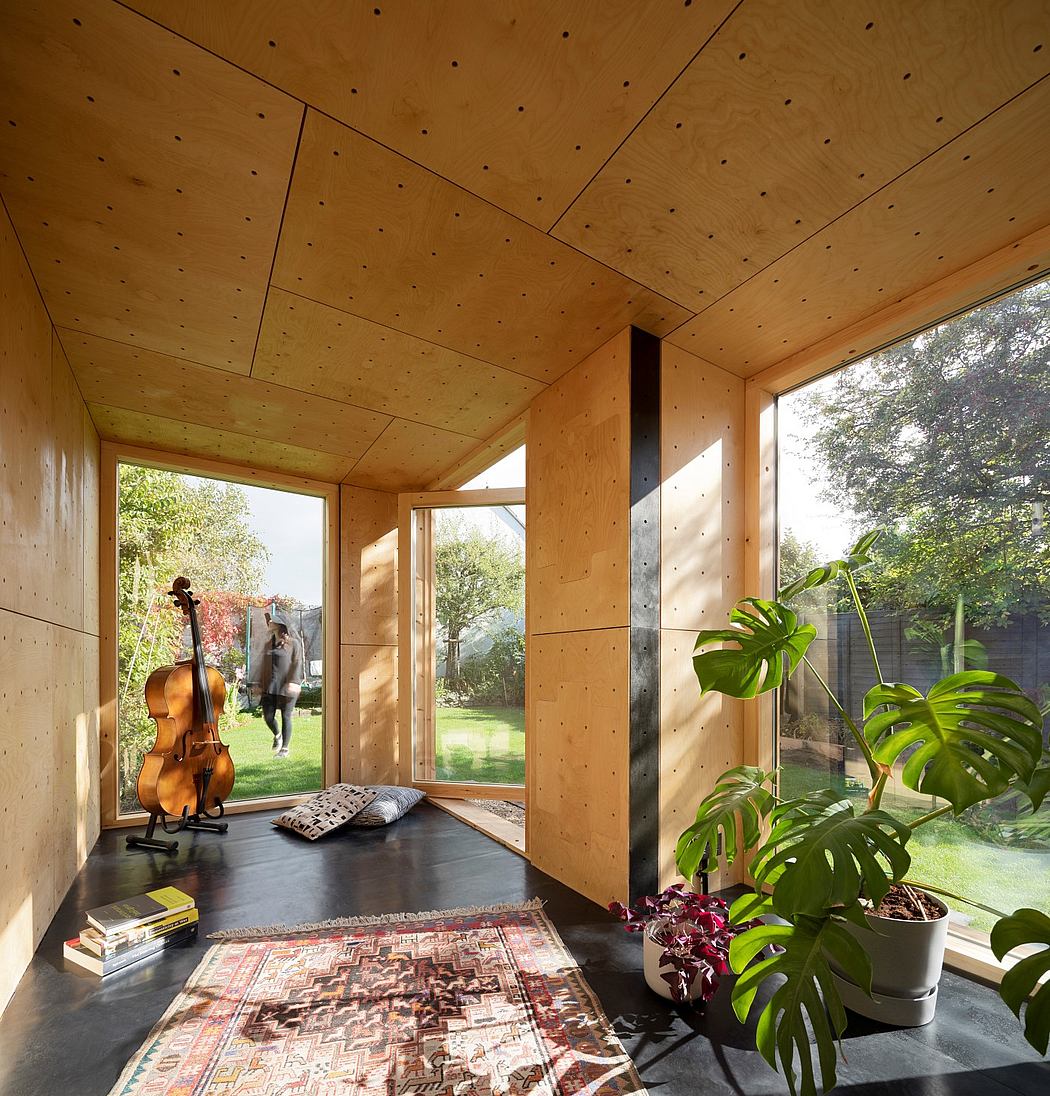
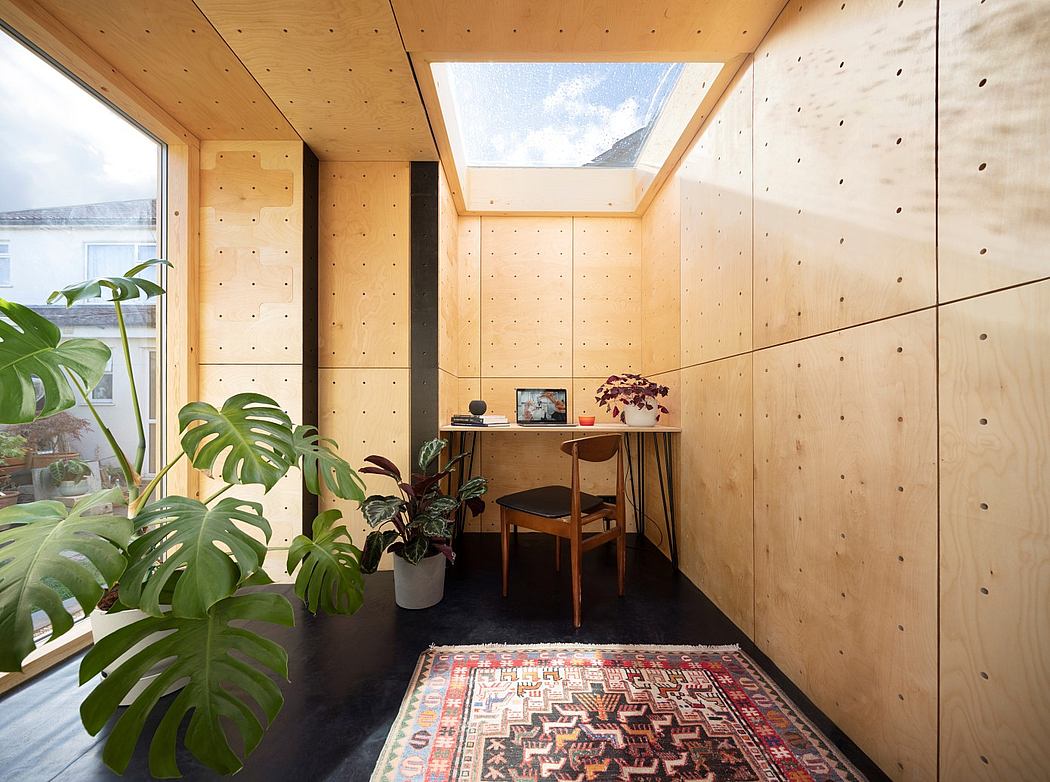
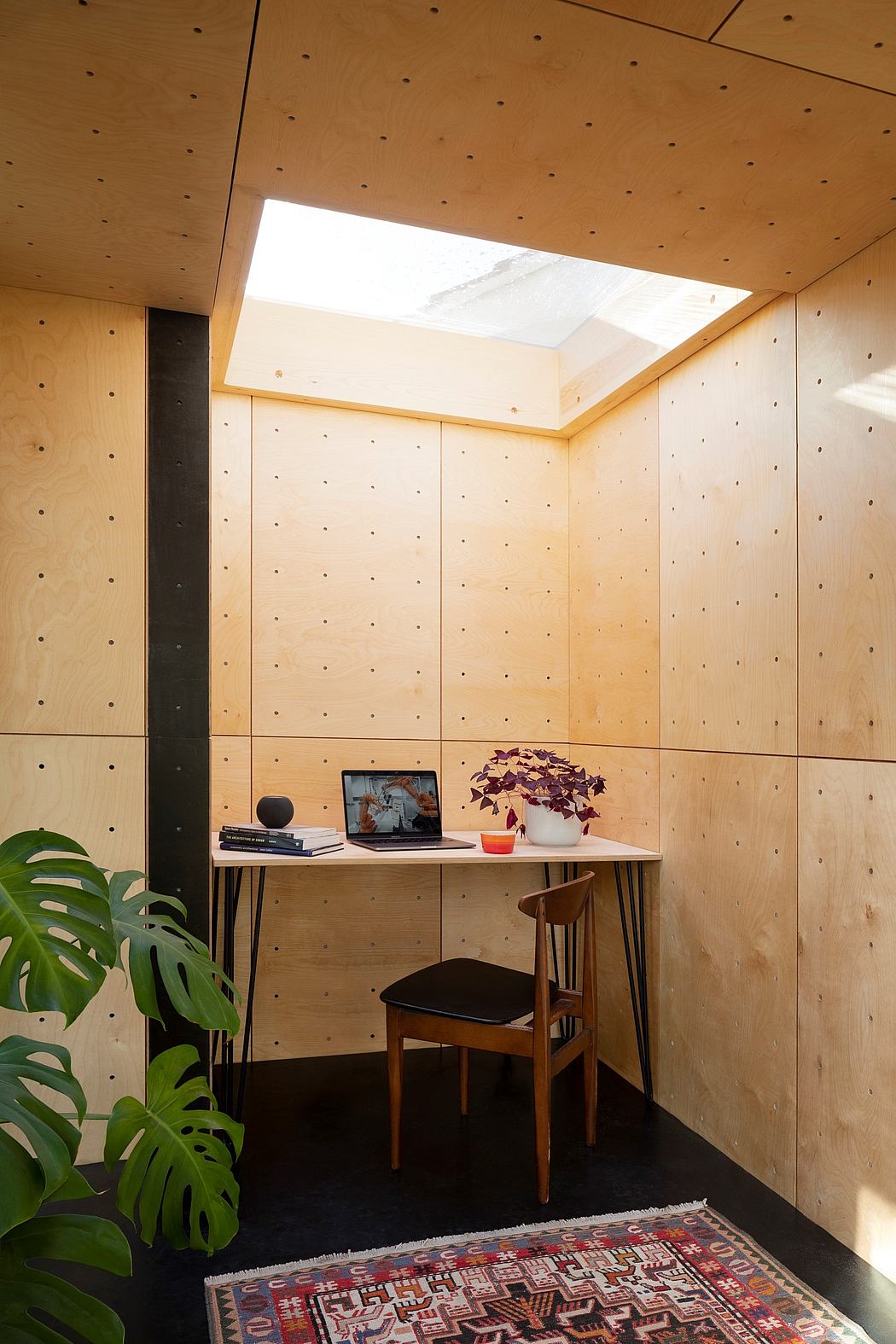
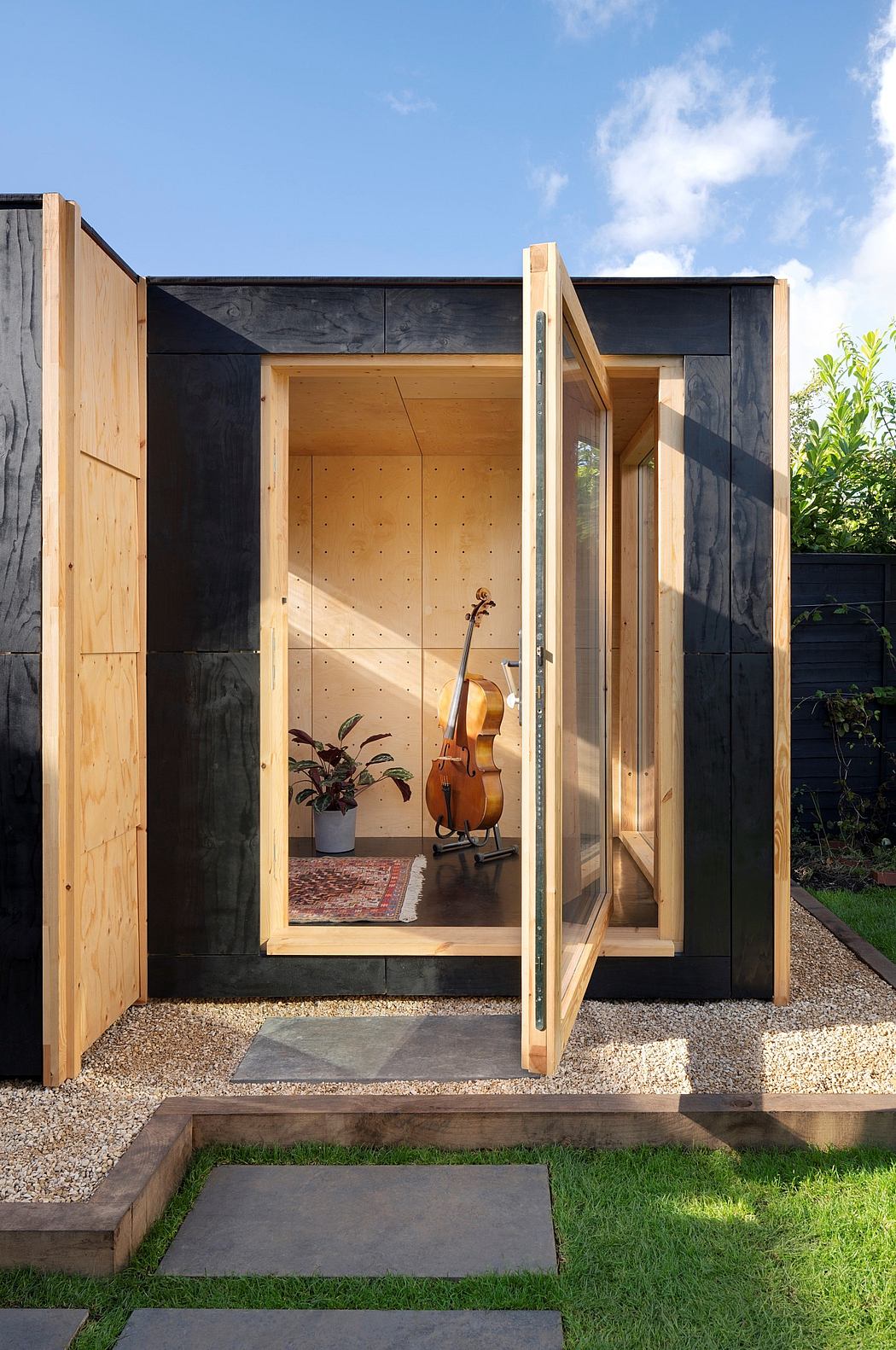
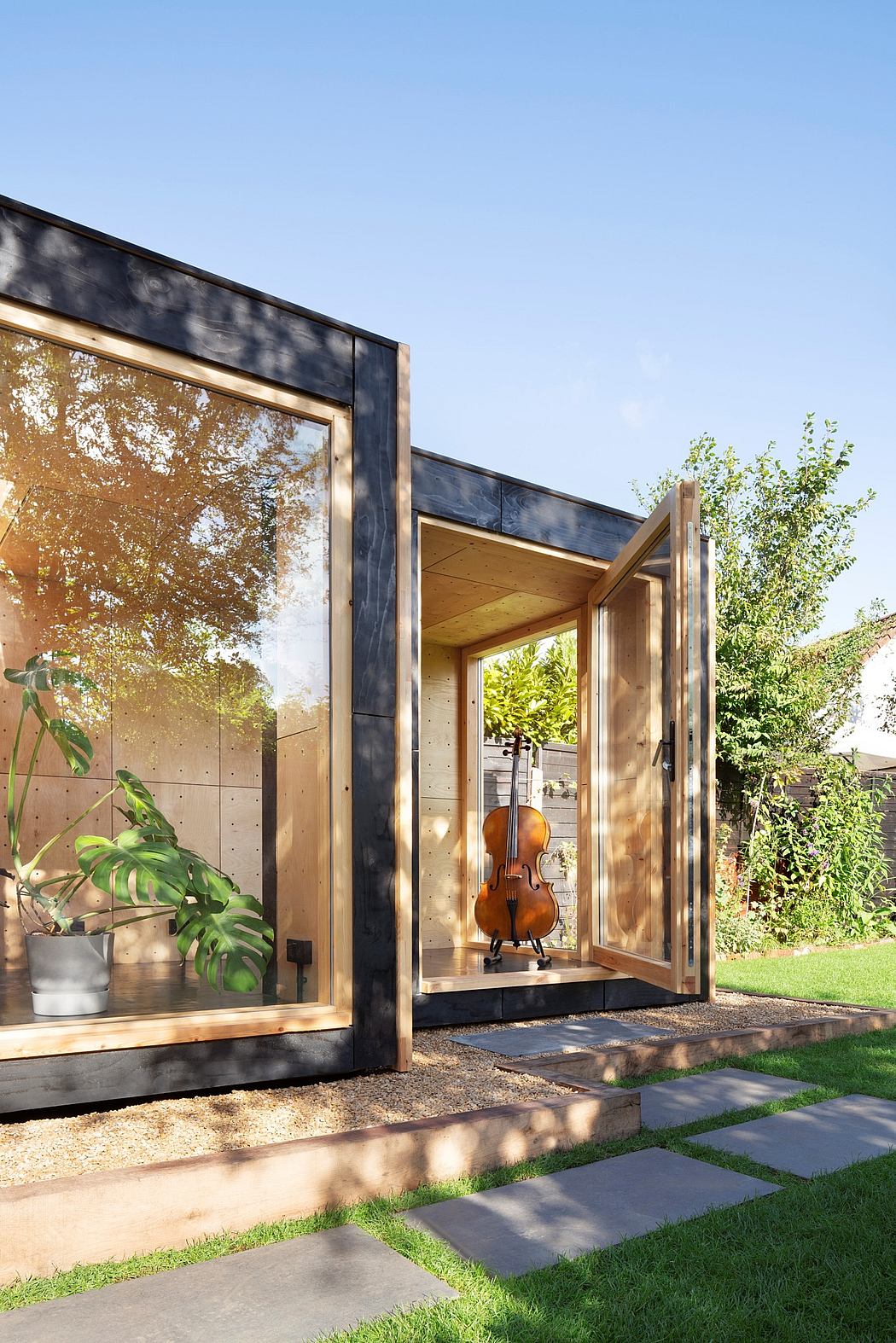
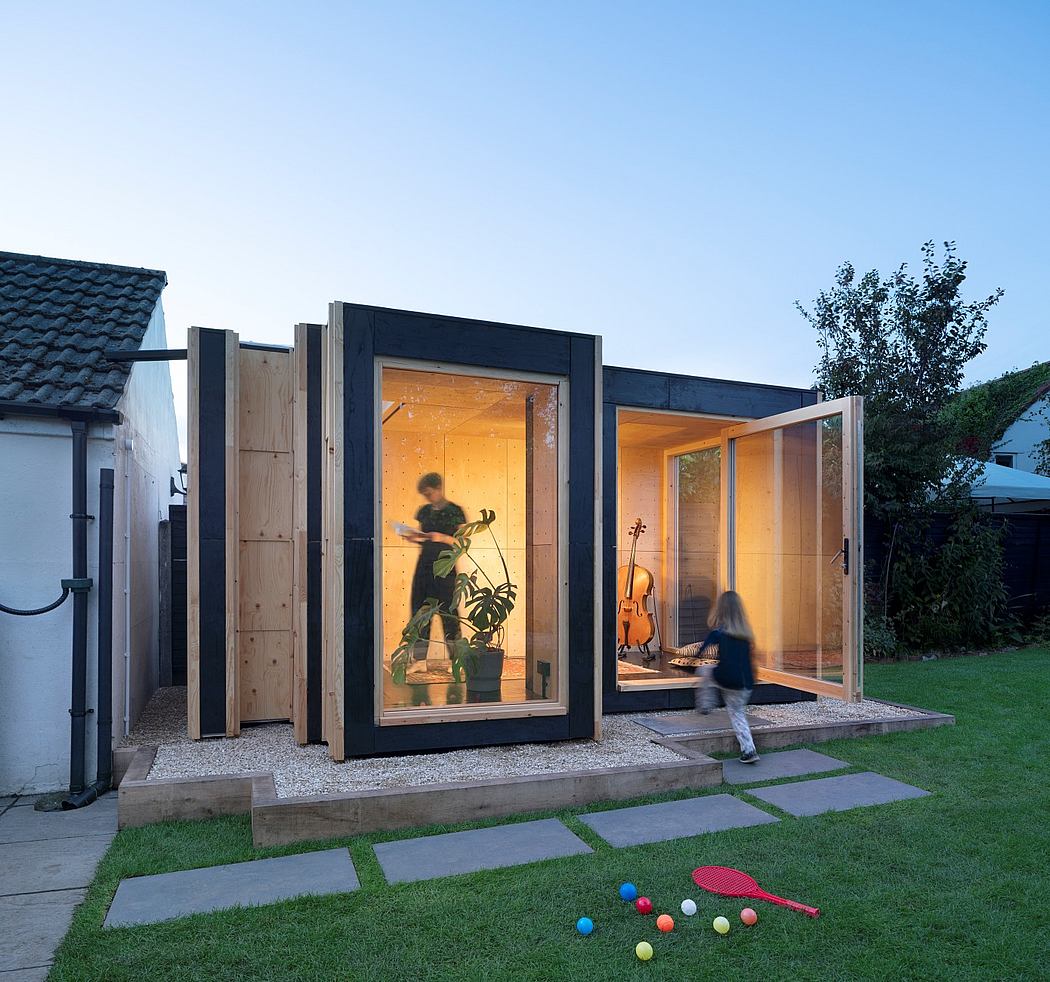
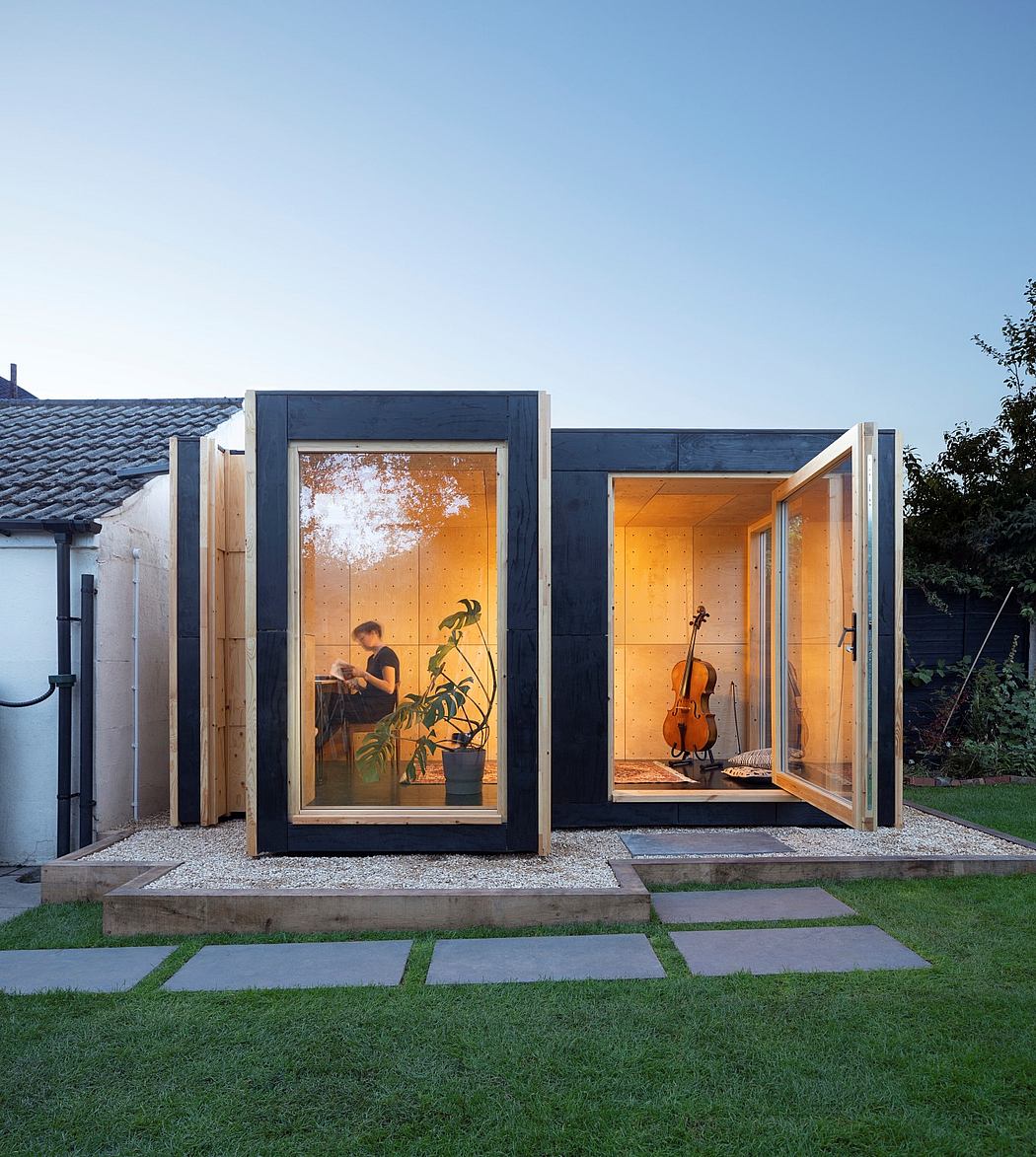
Description
Bristol and London-based design and technology company Automated Architecture Ltd (AUAR) has completed its first permanent dwelling unit: Dwelling Unit for Musicians. At 10 square metres (107 square feet), the dwelling unit is constructed using AUAR’s modular timber building system, which integrates robotics and automation to provide high-quality, beautifully designed, and sustainable affordable housing. In particular, the project demonstrates the potential of AUAR’s system to support customisation and community participation in the construction process.
Based in Bristol, the clients for Dwelling Unit for Musicians are a cellist and double bassist who will use the space as an office and rehearsal studio. They selected AUAR’s system over other backyard-unit options because AUAR’s dwelling units can be easily customized to site and use, offering a unique structure. They also feature thermal and acoustic insulation, which can be achieved while still retaining a light-filled space, as well as renewable properties and a low-carbon footprint.
At its core, AUAR’s modular system consists of building blocks made from timber, a renewable material, which are robotically pre-fabricated and assembled into dwelling units. The production chain begins when a robot assembles timber sheets into individual building blocks, then stacks the blocks into easily transportable units. These units are delivered locally to a given site and assembled by local craftspeople and builders into homes.
Using AUAR’s automation process, the units can be easily customized based on site characteristics and a given inhabitant’s lifestyle and visual preferences. This provides a radical alternative to existing modular housing approaches which are repetitive and difficult to adapt to local contexts. Uniquely, the timber building blocks can be disassembled and reassembled for other uses, therefore creating less material waste and aligning with principles of circular design.
In the case of Dwelling Unit for Musicians, AUAR generated multiple designs in response to the South-East facing building site and an understanding of the clients’ needs. With the same number of blocks, AUAR discussed radically different, customised options. “Some of the designs were more introverted, other block combinations were more open to the garden, whilst others explored the design possibilities of an alcove space, with or without rooflight, and so on,” explains AUAR CEO Mollie Claypool. From there, the clients selected the features they preferred, and a final version was generated. Importantly, the exact cost was known at all times, as it relates directly to the number of blocks used.
Fabrication of the timber components took place locally, in Bristol, at the citizen-led manufacturing hub KWMC The Factory. Block prefabrication took two weeks and the dwelling unit itself was constructed in seven days by a combination of local contractors and community
residents experienced in working with AUAR’s modular building system and employed to work alongside the AUAR team.
The resulting unit fits seamlessly into the client’s backyard. Despite a small footprint of 10sqm (107sf), a large floor-to-ceiling window/door offers a visual and physical connection to the client’s garden, giving an impression of spaciousness. A skylight positioned over the desk enhances the natural light flooding the unit. Along with the timber blocks and timber cladding, all additional construction materials were selected for their low-carbon, sustainable properties. These include a non-toxic, recyclable EPDM roof, rubber floor, and paper cellulose insulation.
Overall, AUAR’s system uses sustainable materials and decentralizes by localizing the fabrication and construction process, instead of importing materials or modular homes from far afield. This simultaneously reduces carbon footprint and increases community involvement.
“For AUAR, people are central to automation. This starts with design. Our homes are not standard, one-size-fits-all spaces, but can be tailored and customized for every unique client, for each specific plot of land. As we use intelligent robotics and automation, it doesn’t cost anything more to make a different home each time,” says CTO Gilles Retsin.
“The importance we place on people extends throughout our short production chain from localized fabrication through to on-site construction, care and maintenance. This ensures that we leverage the benefits of automation in a way that directly adds to local communities, keeping them together when they might otherwise be displaced due to the housing crisis, whilst expanding local skillsets—not detracting from them,” says CCO Claire McAndrew.
The next in AUAR’s series of Dwelling Units is due for completion by the end of December 2021 and showcases a different configuration of blocks. Scaling from small (10-15sqm/107-160sf), through to medium (15-25sqm/160-270sf) and large (25-50sqm/270-540sf), AUAR’s system offers housing that communities need at scales that positively impact daily lives.
Photography by naaro
Visit Auar
- by Matt Watts